Научный журнал "Территория «НЕФТЕГАЗ»", №12, 2017 г. - http://tng.elpub.ru/jour/article/view/652
Качанов О.М., Токарев В.Г., Куреньков А.И., Рыбко Д.В.
Измерение уровня жидкостей в технологических резервуарах является важнейшим элементом в организации современных эффективных технологических процессов, которые встречаются во многих отраслях промышленности (хранение нефтепродуктов, химические процессы, перевозка сжиженных веществ, фармацевтическое производство и др.).
Уровнемеры и сигнализаторы уровня выпускает множество фирм, как зарубежных, так и отечественных.
Существует множество средств контроля и измерения уровня, основанных на различных физических методах: емкостной, электроконтактный, гидростатический, поплавковый, ультразвуковой, радиоволновый, изотопный. Все эти методы, применяющиеся в современных уровнемерах и сигнализаторах уровня, требуют монтажа своих первичных преобразователей внутри контролируемой емкости (исключение составляют изотопный метод ).
Поэтому при выборе средства измерения уровня возникают следующие проблемы:
- приходится учитывать такие физические и химические свойства контролируемой среды, как: температура, абразивные свойства, вязкость, электрическая проводимость, химическая агрессивность и т. д.;
- следует принимать во внимание рабочие условия в резервуаре: давление, вакуум, нагревание, охлаждение, способ заполнения или опорожнения, наличие внутренних механизмов и конструкций, огнеопасность, взрывоопасность и другие;
- невозможность, нежелательность или сложность изменения проектной конструкции резервуара для некоторых специфических случаев, например для резервуаров высокого давления, резервуаров содержащих особо опасные вещества либо при особо чистых производствах.
Кроме того, к приборам измерения уровня заполнения ёмкостей и сосудов предъявляются различные требования: в одних случаях требуется только сигнализировать о достижении определённого предельного значения, в других - необходимо проводить непрерывное измерение уровня заполнения. Поэтому существует две группы приборов контроля - это уровнемеры и сигнализаторы уровня, которые различаются функционально и относятся к разным ценовым категориям.
Создание сигнализатора с функциями уровнемера является актуальной задачей позволяющей повысить удобство и достjверность некоммерческого контроля уровня жидкостей.
Компанией ООО «НПП-Техноавтомат» разработан неинвазивный ультразвуковой сигнализатор уровня жидкости «Рубин-1М», работа которого основывается на возбуждении и приеме ультразвуковыми датчиками в стенке контролируемого резервуара (технологического аппарата) с ее наружной стороны зондирующей волны Лэмба, т.е. упругой ультразвуковой волны, в которой колебательное смещение частиц происходит как в направлении распространения волны, так и перпендикулярно плоскости стенки. Степень затухания амплитуды волны Лэмба определяется расстоянием, пройденным волной по стенке резервуара, а также поглощением ее энергии окружающей средой, с которой контактирует эта стенка. Последнее в значительной степени зависит от свойств этой среды. Поглощение энергии жидкостью в разы отличается от поглощения ее воздушной средой.
В работе сигнализатора «Рубин-1М» используется это свойство разности степеней затухания волны Лэмба при контакте стенки с разными средами (газ и жидкость), которое реализуется через возбуждение зондирующей акустической волны по разным каналам, в том числе дублирующим друг друга, и комплексный анализ различных параметров возбужденной волны, результаты которого в сумме дают достоверную информацию как о граничных положениях уровня жидкости (функция сигнализатора), так и о динамике изменения уровня жидкости (функция уровнемера).
Волновой процесс, возникающий при возбуждении ультразвуковых колебаний в тонких пластинах, которыми и являются стенки сосудов представляет собой неоднородную нелинейную конфигурацию группы нормальных волн, которые описываются следующими уравнениями:
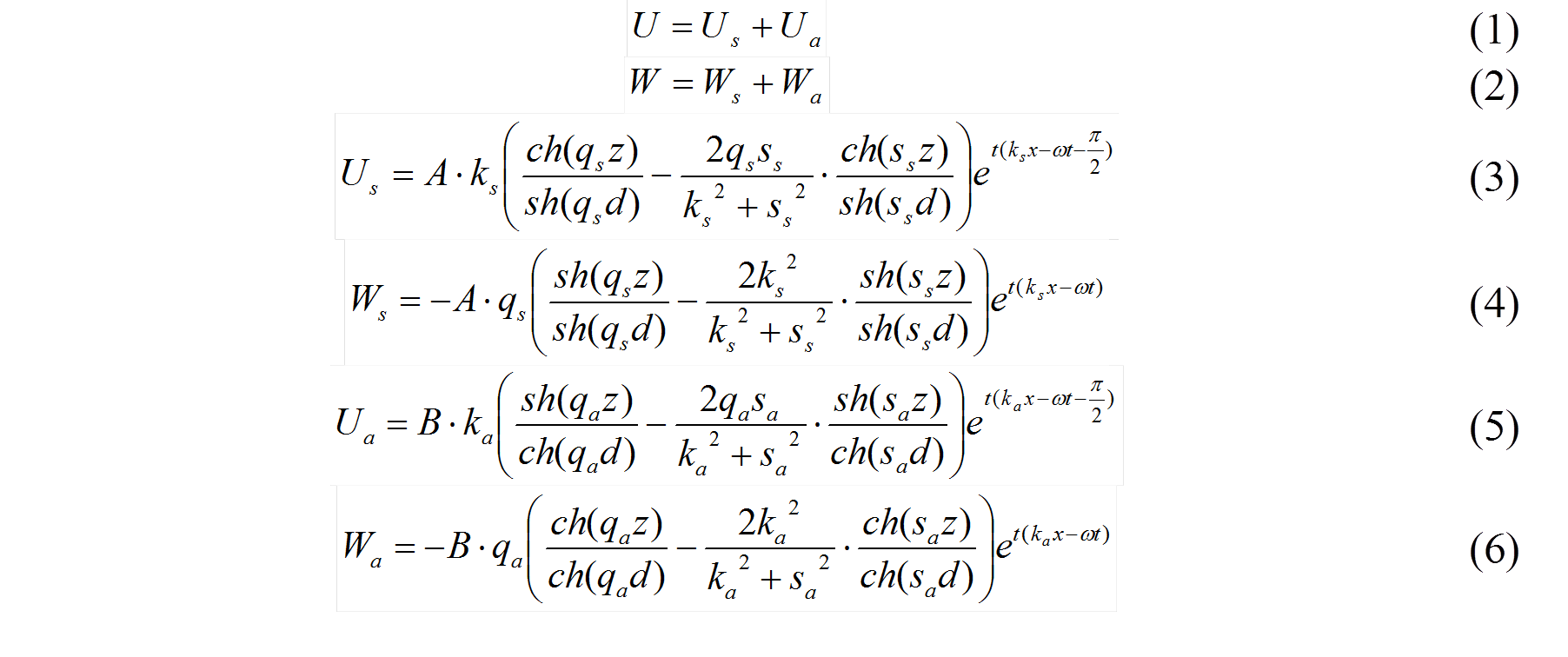
где U, W – компоненты общего продольного и поперечного смещений, соответственно; Us, Ua – компоненты продольного смещения, относящиеся к симметричной и антисимметричной волне, соответственно; Ws, Wa – компоненты поперечного смещения, относящиеся к симметричной и антисимметричной волне, соответственно; A, B – произвольные постоянные, определяемые начальными условиями возбуждения; z – поперечное положение точки относительно серединной плоскости пластины; d – толщина пластины; x – расстояние вдоль пластины; ω – круговая частота колебаний; t – время; k, q, s – волновые числа, связанные соотношениями:

где ks,a – волновые числа, относящиеся к симметричной и антисимметричной волнам, kl, kt, – волновые числа, относящиеся к продольной и поперечной волнам, соответственно. Анализ уравнений показывает, что большая часть энергии для антисимметричной волны сосредотачивается в поперечных колебаниях, тогда как для симметричных, наоборот – в продольных. Аналитическое решение задачи определения степени поглощения волн Лэмба разных видов для конкретных условий достаточно сложное. Однако характер этой зависимости просматривается уже на соотношениях коэффициентов затухания волн Рэлея, которые в наибольшей степени схожи с волнами Лэмба нулевых мод, вырождающихся в них при d>>λR, где λR – длина волны Рэлея. Наибольший вклад в коэффициент затухания волн Рэлея вносят поперечные волны. Аналитическая зависимость для коэффициента затухания выражается следующей формулой:

где α – коэффициент затухания продольной рэлеевской волны, β – коэффициент затухания поперечной волны Рэлея, A – некая величина, зависящая только от свойств материала, выражаемая через коэффициент Пуассона ν. Для стали, например, приведенное выше выражение приобретает следующий вид: γ = 0,11α + 0,89β. Последнее свидетельствует о том, что затухание этих волн определяется в большей степени поперечной составляющей.
Прибором «Рубин-1М» для контроля уровня жидкости используется симметричная волна Лэмба нулевой моды, в качестве опорной, и антисимметричная волна Лэмба нулевой моды, в качестве основной, как наиболее информативная для данного процесса. Данный принцип зарегистрирован как технология измерения TechnoLamb.
Существенным преимуществом прибора «Рубин-1М», которое позволяет решить проблемы, препятствующие применение других приборов измерения уровня, основанных на ином принципе работы, является его способность работать в тяжелых промышленных условиях, осуществляя контроль различных агрессивных или особо чистых веществ, исключая при этом влияние внутренних конструкций и процессов внутри емкости. Это обеспечивается именно при неинвазивном методе контроля ультразвуковых волн, распространяющихся в стенках различных резервуаров, открытых и закрытых (толщиной стенки до 70 мм).
Также, благодаря оригинальным инженерно-конструкторским решениям достигнута ценовая доступность, компактность, простота монтажа и удобство в эксплуатации прибора, в котором реализованы функции самодиагностики и автонастройки.
По техническим требованиям и по результатам испытаний на объектах ПАО «АК Транснефть» на базе регистратора уровня «Рубин-1М» была разработана новая модификация прибора «Рубин-1М-НП», которая предназначена для контроля уровня нефти в нефтепроводах и других аппаратах, таких например, как приемные и выпускные камеры очистных снарядов (скребков, РГК). Отличительной особенностью данной модификации является то, что она позволяет не просто фиксировать некоторые предельные значения уровней, как в «Рубин-1М», а определяет положение уровня по всему профилю сечения трубопровода и одновременно фиксирует моменты прохождения очистных снарядов и ГРК по трубопроводу. Фиксация момента прохождения очистного снаряда или ГРК осуществляется сразу по двум факторам: по возрастанию/спаду уровня акустических шумов и по резкому перепаду измеренного уровня нефти в трубопроводе. Данный прибор позволяет контролировать и производить оценку размеров газовых пробок, которые возникают при наполнении трубопроводов нефтью или ее вытеснении азотными установками, во время прохождения очистных снарядов или ГРК по трубопроводу, а также определять остаточный уровень нефти в трубопроводе после его освобождения. В приборе «Рубин-1М-НП» реализованы многоканальные измерения ультразвуковых сигналов сразу на нескольких участках по контуру сечения трубопровода. На это техническое решение получен патент РФ на изобретение № 2608343 от 31 июля 2015 г. «Способ контроля уровня жидкости в резервуарах по характеристикам волн Лэмба и устройство для его осуществления».
Схема контроля, реализованная в приборе «Рубин-1М-НП» позволила, путем анализа соотношений уровней сигналов на разных участках, автоматизировать процесс настройки прибора и его калибровку сразу же при его установке на объект. При запуске прибора оператор задает лишь параметры объекта: диаметр трубопровода и толщину его стенки, тип изоляции и вид жидкости в трубе. Остальные измерительные параметры (коэффициенты усиления измерительных каналов, коэффициенты затухания сигналов по измерительным участкам и начальные уставки уровней сигналов по «газу» и «жидкости») прибор определяет сам.
Процесс измерения начинается с того, что вначале, по соотношению уровней сигналов на разных участках окружности профиля трубопровода относительно определенных уставок уровней по «газу» и «жидкости», вычисленных при калибровке, определяется грубо, на каком участке находится уровень. Затем, вычисляется значение длины дуги окружности участка, соприкасающегося с жидкостью. При этом используется логарифмическая аппроксимация функции затухания ультразвукового сигнала волны Лэмба.

где: Lж – длина дуги соприкасающейся с жидкостью для соответствующего из мерительного канала; K – приведенный коэффициент затухания сигнала (определяется при калибровке, автоматически); А – текущая амплитуда сигнала; UГ – уставка амплитуды по газу. По найденной длине дуги, соприкасающейся с жидкостью, в соответствие с геометрией ее расположения на окружности сечения трубопровода вычисляется и текущее положения уровня жидкости в нем. Для примера на рис.1 приведено схематичное сечение трубопровода, схема расположения датчиков на стенке трубопровода и схема расчета уровня жидкости.
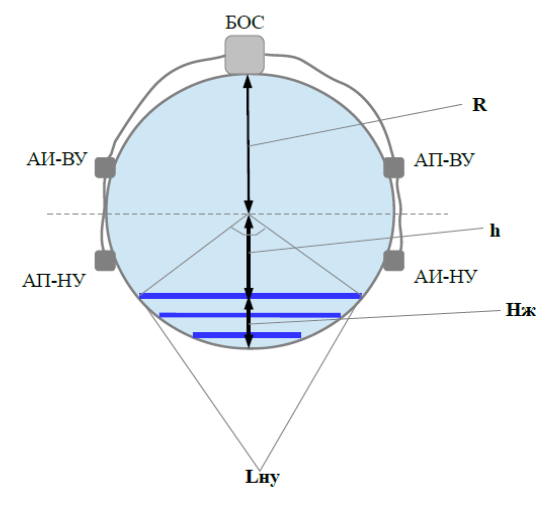
Рис. 1. Схема расположения датчиков и расчета уровня жидкости в трубопроводе.
БОС – блок обработки сигналов, АИ-ВУ – акустический излучатель верхнего уровня, АП-ВУ – акустический приемник верхнего уровня, АИ-НУ – акустический излучатель нижнего уровня, АП-НУ – акустический приемник нижнего уровня, R – внутренний радиус трубопровода, h – расстояние от середины трубопровода до уровня жидкости, Hж – уровень жидкости, Lну – дуга жидкости на нижнем канале измерения.
Одновременно с определением положения уровня жидкости в трубопроводе или другом закрытом аппарате круглого сечения прибор осуществляет контроль акустических шумов, возникающих в стенке участка трубопровода, где установлены датчики прибора. Такой контроль позволяет надежно отследить не только текущий уровень наполнения трубопровода жидкостью, но и момент прохождения самого очистного снаряда, а также обнаружить «свист» запорной арматуры приемно-выпускных камер, в случае нарушений их герметичности и появления возможных утечек. Таким образом, фиксация повышения уровня акустических шумов и возникновение провалов измеряемого уровня, позволяет значительно повысить надежность такого комбинированного контроля.
Уникальность технологии, основанной на контроле волн Лэмба позволила обеспечить многофункциональность в одном приборе и значительно повысить его эффективность при контроле герметичности камер приема-пуска в сравнении с уже имеющимися приборами, такими например как ДГК-1-3д.
В настоящее время прибор успешно прошел ряд технологических испытаний в промышленных условиях на объектах ПАО «Транснефть». Подготовлен мобильный переносной вариант прибора, который может автономно использоваться в полевых условиях, как для контроля на участках магистрального нефтепровода, так и других технологических аппаратах ПАО «Транснефть». Ведутся работы по сертификации прибора и патентованию в странах ЕС. Фотография прибора «Рубин-1М-НП» мобильного исполнения и результаты последних испытаний на объектах представлены на рисунках ниже.
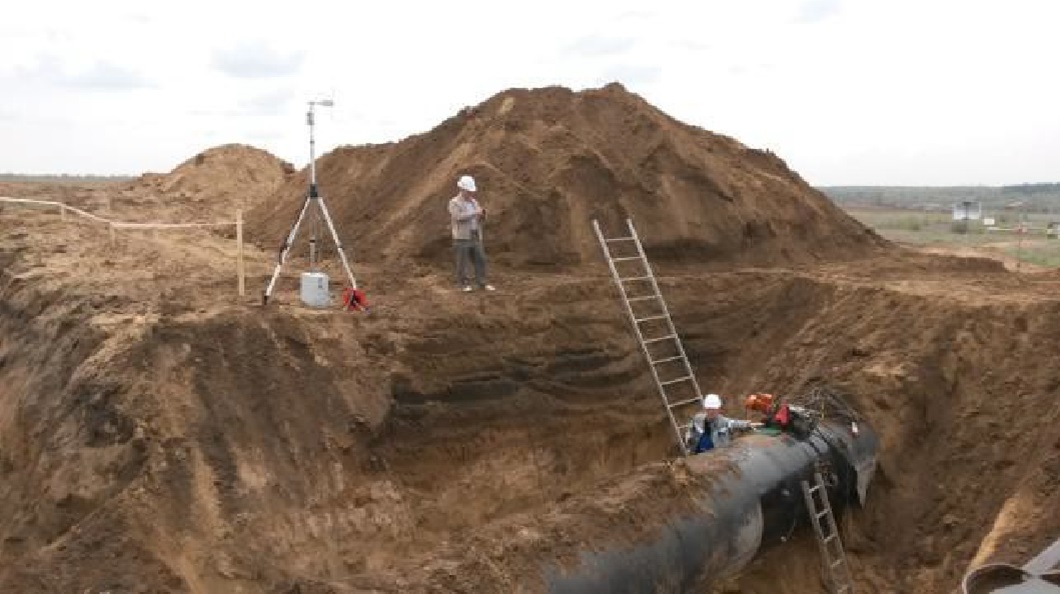
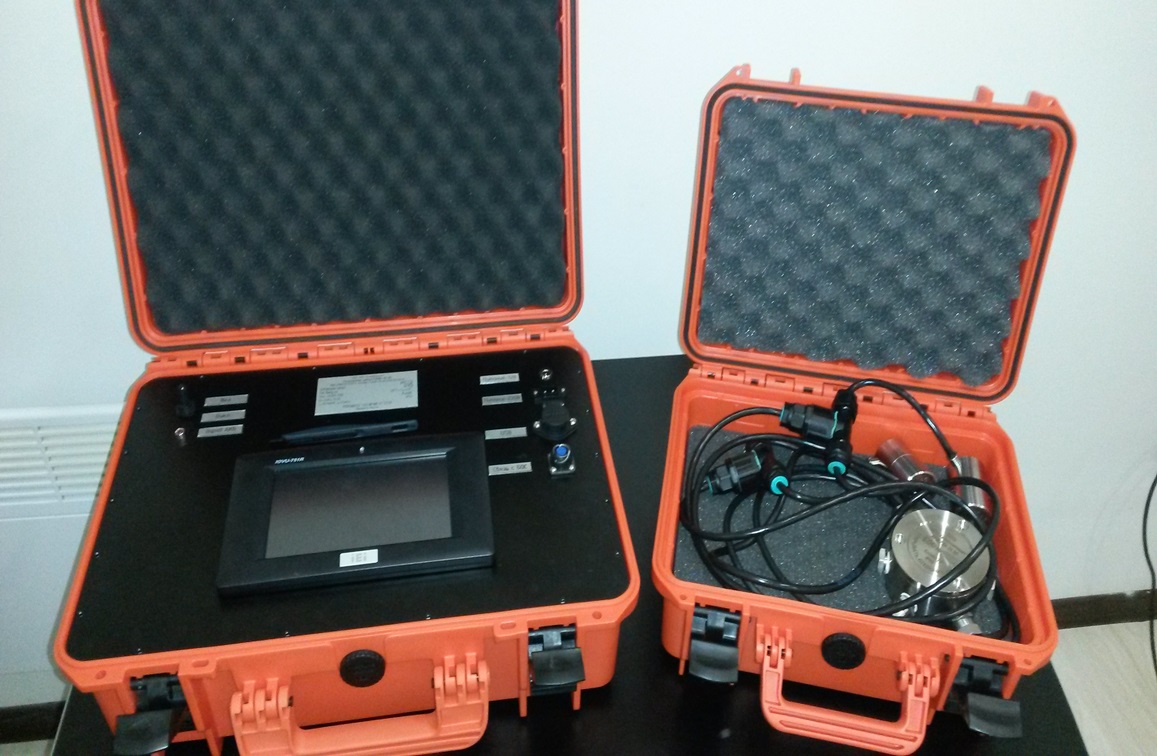
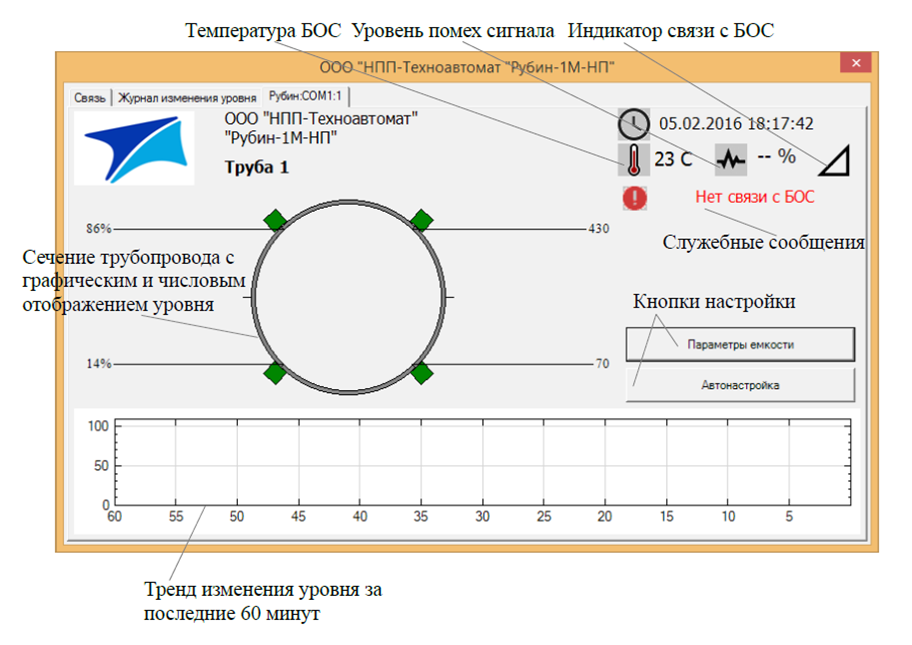
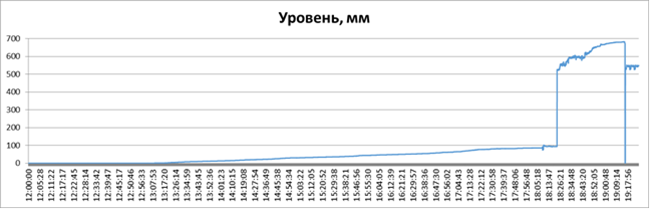
Рис.2. График изменения уровня нефти в контрольной точке нефтепровода. По оси Х – время в формате ЧЧ:ММ:СС, по оси Y – уровень в мм
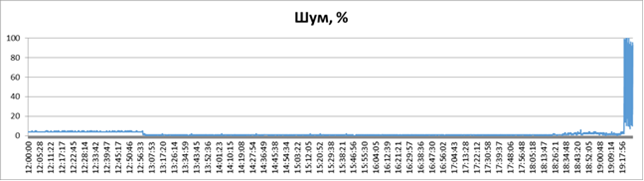
Рис.3. График тренда изменения уровня шумов в контрольной точке нефтепровода.
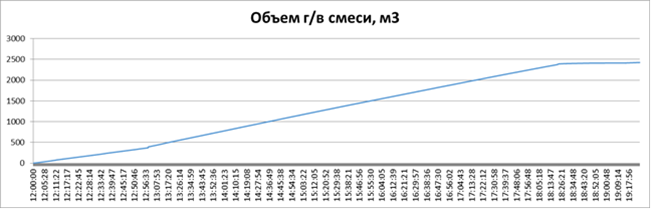
Рис. 4. График расчетного объема газовоздушной смеси прошедшей через сечение трубы (при условной скорости поршня, принятой равной 1 км/ч). По оси Х – время в формате ЧЧ:ММ:СС, по оси Y – объем г/в смеси в м3.
По средней скорости движения ГРК по трубе вычисляется примерный объем газовоздушной смеси, прошедшей через сечение контролируемого участка трубы, по следующей формуле:

где: V – текущий объем газа прошедший через сечение трубы; V0 - объем газа прошедший через сечение трубы в предыдущий момент времени; U – средняя скорость поршня, ГРК; t – текущий момент времени, t0 – предыдущий момент времени; R – внутренний радиус трубы; L – текущий уровень нефти в трубе; Зная давление на данном участке трубы, можно привести объем газа к нормальным условиям.
Выводы:
1. Применение неинвазивной ультразвуковой технологии контроля распространения волн Лэмба в стенках резервуаров позволило обеспечить комбинированные измерения нескольких технологических параметров в одном приборе, а именно:
- измерять уровень нефти в трубопроводе с точностью до 5% от его диаметра c автоматической калибровкой;
-определять прохождение очистного снаряда или ГРК с высокой достоверностью;
-фиксировать прохождение газовых «пузырей» по трубопроводу и производить оценку их размеров;
-диагностировать утечки по шумовому спектру сигнала.
2. Применение схемы контроля реализованной в приборе «Рубин-1М-НП» позволяет существенно повысить качество и достоверность мониторинга техпроцесса транспортировки нефти по трубопроводам.
3. Следует отметить и экономическую эффективность прибора, т.к. по сути один прибор реализует несколько функций, очень прост и удобен в эксплуатации.
4. Уникальные возможности данного способа контроля позволяют прогнозировать его широкое внедрение в различных отраслях промышленности в РФ и за рубежом.
Авторы:
Качанов Олег Михайлович – генеральный директор ООО «НПП-Техноавтомат»
Токарев Вячеслав Григорьевич - главный инженер ООО «НПП-Техноавтомат»
Куреньков Антон Иванович – ведущий инженер ООО «НПП-Техноавтомат»
Рыбко Денис Вячеславович – ведущий инженер АСУ ТП АО «Транснефть-Приволга»